RuniOne: Quality Management System Construction
Quality is the foundation of our company and the primary concern for our customers. How can we provide products and services that satisfy our customers? How can we maximize the value of the quality management system in our company's management? How can the quality management system support the achievement of our business goals? These are the questions that the managers and quality personnel at RuniOne always contemplate.
Since the establishment of our company, the senior management at RuniOne has been dedicated to implementing ISO9001 standards. Through scientific planning and systematic organization of work processes, as well as the clear assignment of job responsibilities and coordination between departments, we have established a comprehensive quality management system. RuniOne Shanghai and RuniOne (Henan) have both been awarded ISO9001 quality management system certification and ISO14001 environmental management system certification by SGS/TUV.
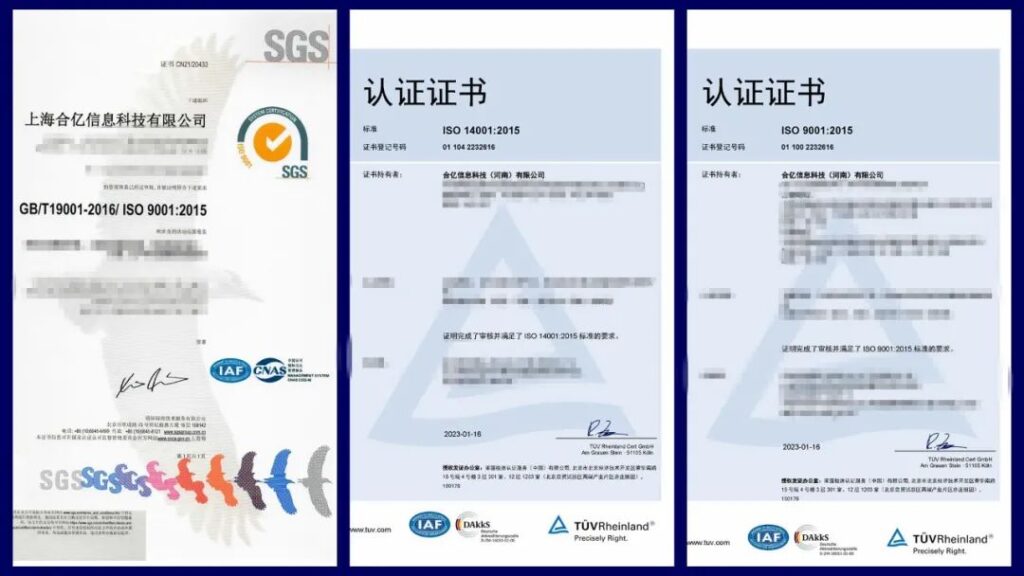
It is a common phenomenon in the industry that after the establishment of a quality management system, it is often overlooked as it is perceived to have no direct contribution to company profits.
Fortunately, the senior management of RuniOne deeply understands the importance of quality system work and insists on practicing the quality policy: "Leading Professionally, pursuing customer satisfaction with better quality service; pursuing excellence, achieving company development through rigorous process management." The company always prioritizes customer needs, satisfies them with technologically advanced intelligent terminal products, and achieves excellence through a rigorous process control system and product services.
ISO 9001 standard, as an exemplary scientific management method, not only serves as a guide to enhance the scientific management level of companies but also as a platform for promoting innovation in management methods. Strengthening the construction of the quality system and continuous improvement have become the norm in management. Through various means of promotion, the work method of continuous improvement through the PDCA cycle has been deeply rooted in the hearts of the people at RuniOne. At RuniOne, the PDCA cycle is not only reflected in the stage of process formulation but also in the work methods of employees. Every task is planned before implementation, checked during implementation, and improved based on the check results. Through continuous positive cycles and a self-improving long-term mechanism, the vitality and sustained robustness of the company's quality management system are maintained.
The Quality Management Department takes the continuous collection of pain points in various departments, optimizes and improves efficiency, organizes process training, and promotes process execution as routine work. Each department learns from peers and customers to gather better management experiences for sharing. The company encourages innovation from all employees through innovative mini-programs, including process innovation and management innovation. Everyone participates, seizing every opportunity for process optimization.
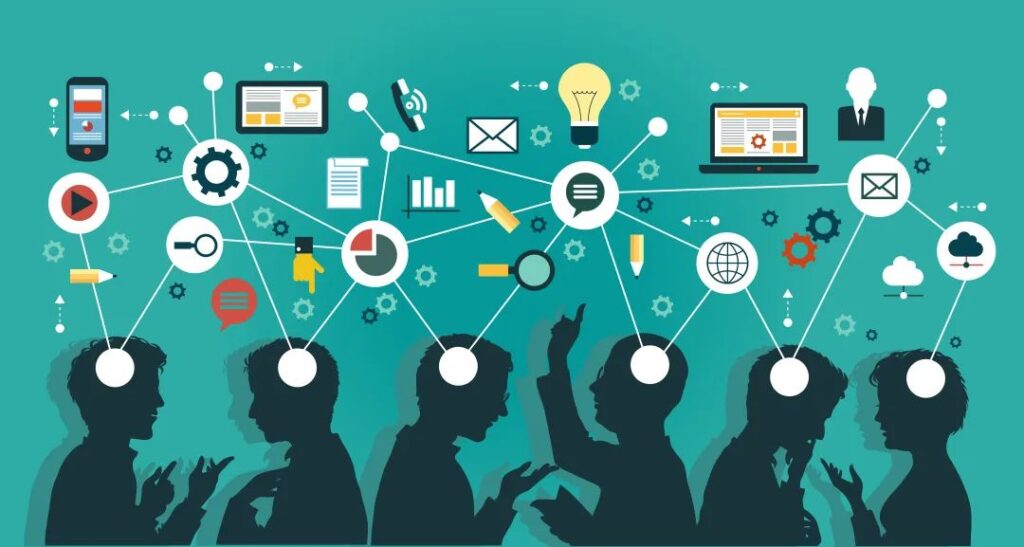
Since 2022, through the efforts of various departments, 19 new and revised process documents, as well as 30 related forms, have been added. The main focus of optimization includes:
- The Business Department has developed the "Trade Compliance Inquiry and Risk Mitigation Process" specifically for overseas operations.
- The Quality Department has established the "Customer-Supplied Material Management Process" and "Customer-Supplied Software Management Process" in response to the increase in customer-supplied materials. To strengthen control over factory quality, the "DOA (Defect on Arrival) Handling Process" has been developed.
- The Research and Development Department has strengthened R&D management and internal review mechanisms. The Hardware Department and the Structural Department have streamlined design drawing review checklists and key material verification requirements. The Software Department has established the "Code Design Standards" and "Code Review Process."
- The General Administration Department has strengthened the management and encouragement of intellectual property rights, improved the hierarchical management of various trainings, and network security management. They have formulated the "Regulations and Incentives for Patent and Software Copyright Management," "Network Security Management System," and revised the "Training Management System."
- The Product Department has strengthened the management and control of product changes and improved the "Product Change Control Process" and other related processes. All departments and employees of the company have contributed to the enhancement of the quality management system.
Since the establishment of the quality management system, the company has achieved some accomplishments and highlights on the path of continuous improvement:
1."Skillful in extracting data indicators, winning with quality, and system improvement."
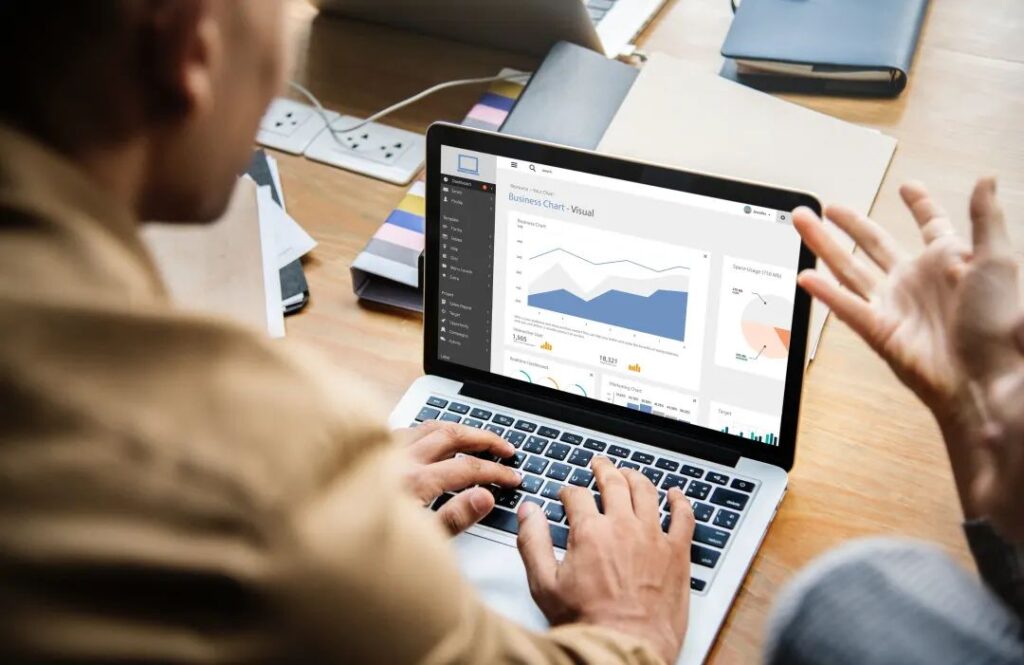
RuniOne attaches great importance to setting quality objectives, statistical analysis of data, and timely adjustment of quality objectives to improve management and product quality. Through monthly quality dashboards and monthly quality meetings, the achievement of quality objectives is monitored. Any deviations or identified abnormal trends are promptly analyzed for root causes and appropriate improvement measures are implemented. Lessons learned are applied to process improvements and knowledge accumulation.
By developing the 3K3T performance management indicators, quality objectives are broken down to department and employee performance levels. Regular reviews and detailed performance management contribute to the achievement and improvement of quality objectives. The after-sales repair rate has decreased from 2.09% in 2021 to 0.93% in 2022. Through management reviews, the achievement of last year's quality objectives was assessed, and this year's quality objectives were adjusted accordingly. These objectives include on-time delivery rate ≥85%, customer return repair rate <1%, personnel punctuality rate ≥80%, after-sales repair qualification rate ≥98.8%, and after-sales repair timeliness rate ≥97.7%. The company continues to identify improvement opportunities from data and strives for system improvement.
2."Customer first, implementing the 1-3-10 and iron triangle service mechanisms"
RuniOne places customers as its focal point and revolves around the three axes of product, delivery, and sales to serve customers. It is committed to creating industry-leading products, competitive delivery, and implementing the 1-3-10 rapid response mechanism for customer complaints (which involves confirming the issue within 1 working day of receiving the complaint, providing preliminary analysis progress within 3 working days, and completing root cause analysis and solution within 10 working days). The on-time handling rate of customer complaints has increased from 69.7% in 2021 to 82.3% in 2022.
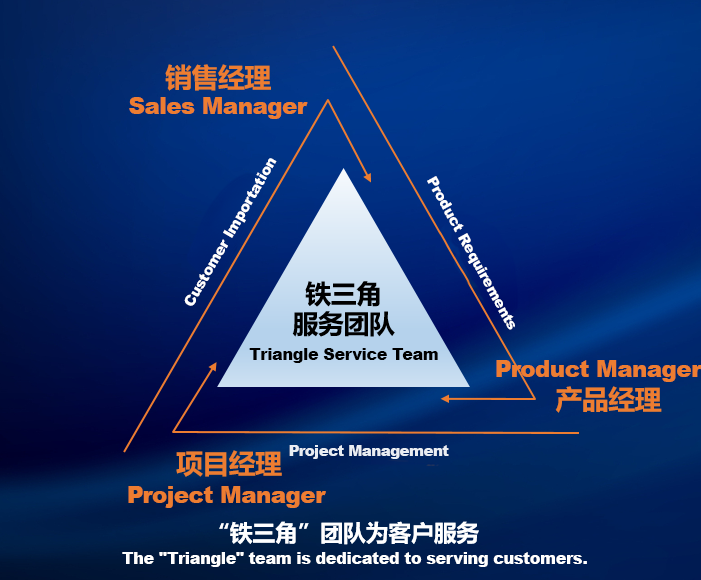
To continuously improve customer satisfaction, in addition to the annual customer satisfaction survey, RuniOne launched a customer feedback system in March 2022. Business personnel can submit customer complaints online at any time, and the Quality Department follows up to resolve them. This year, to improve the timeliness of resolving customer complaints, the 1-3-10 tracking and supervision mechanism has been implemented in the system. The Software Department is currently working intensively on system upgrade and development. We look forward to the new system being launched by the end of June, ensuring that any customer complaints receive timely handling and response, and making every effort to ensure customer satisfaction.
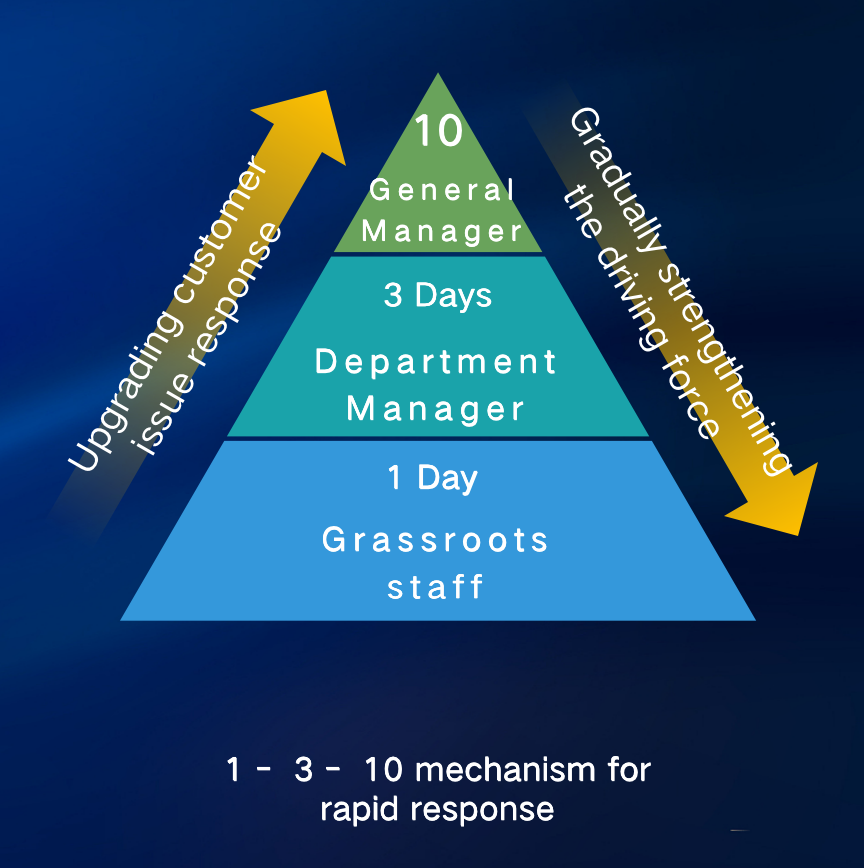
RuniOne will continue to implement the quality policy and quality objectives, meet customer requirements, enhance customer satisfaction, and achieve the company's vision of becoming a leading provider of robust intelligent terminal solutions globally. This will be accomplished through strict process management and continuous improvement mechanisms.